Air Compressor Filter Usage and Maintenance
Compressed air filtration plays a hugely important role in any compressor installation. Having a high-quality air compressor filter will protect your system from particulates, dirt, dust, solid particles, and oil. Harmful contaminants like these can cause damage to your equipment and downstream machinery, wearing down parts and causing blockages.
Without a filter, contamination can even affect your manufactured product, causing loss of production and inevitably landing you with a hefty bill. Therefore, it is essential that high performing filters are used. Poor quality filters may offer a reduced performance, leading to large pressure drops and increasing your energy bill.
To protect your investment and end product, and to guarantee clean, contaminant-free compressed air, we recommend the CompAir filtration range.
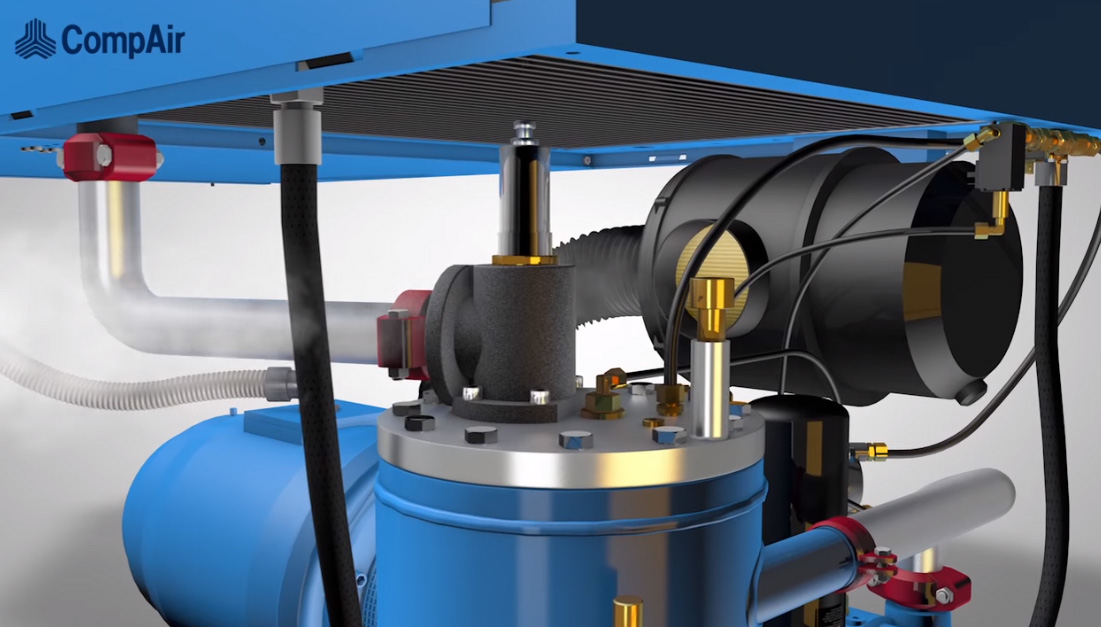
What are the benefits of regularly changing filter elements?
To ensure a continuous supply of high-quality compressed air is always available (and to help keep energy costs low) filter elements must be replaced periodically as, unfortunately, filter elements do not last forever.
The filter element should be exchanged at least every 12 months. Applications with higher annual operating hours or a very high requirement of purification require shorter exchange intervals.
Why do air filters need to be replaced?
- During operation, compressed air filters function under extremely arduous conditions:
- Pressure variations
- Pulsing air demand
- Temperature variations – day/night & summer/winter
- High/low humidity – from 100% saturated air to extremely low dewpoints
- Chemical attack – from oily acidic condensate and lubricant additives
Over time, these extreme and changing conditions can lead to a loss of effectiveness and reduced operational performance, even leading to product spoilage. To continue to perform in even the most challenging conditions, a reliable and durable filter is paramount.
One of the main reasons customers choose not to change filter elements is the cost of replacement parts and maintenance. However, the cost of insufficient filtration is often a multiple of the cost of a filter element!
Not changing the filter can seriously damage your compressed air system as well as your air accessories and downstream products. This results in reduced performance, higher costs, and risk of breakdown.
Not changing the filter element can cause:
- Corrosion of equipment after the filter
- Contamination of the network results in damaged products and end-use contamination
- Reduced availability / damaging of production machinery causing downtime
- Increased long-term costs
For maximum performance, cost-effectiveness, and energy efficiency, air compressor filters need to be replaced as per the manufacturer’s instructions. Proper use results in great energy savings for business owners.
Through usage, more and more particles will attach to the filter medium, reducing the surface for air to flow through the filter. The pressure drop increases, meaning that the overall system costs more to run. For optimised energy saving and high efficiency, it’s important to exchange the filter after the recommended period of time.
Watch this video to learn more about how important it is that the air filter is replaced with a genuine CompAir filter, to prevent damage to your compressor installation:
Differential pressure gauge on a compressed air filter